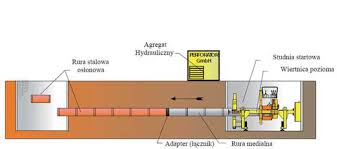
Mikrotuneling – bezwykopowa technologia budowy kanalizacji sanitarnych i deszczowych w terenie o intensywnej zabudowie, eliminująca do minimum zakłócenia w ruchu ulicznym i dewastacje istniejących nawierzchni.
W technologii tej można wyróżnić trzy etapy pracy:
- Wiercenie pilotażowe,
- Rozwiercanie gruntu,
- Przecisk hydrauliczny rur przewodowych.
W czasie pierwszego etapu w zaplanowanej osi rurociągu odbywa się przecisk hydrauliczny żerdzi pilotowych, zakończonych głowicą pilotową. W etapie tym grunt jest zagęszczany wokół żerdzi i nie ma potrzeby usuwania urobku. Kierunek przecisku podlega stałej kontroli i może być korygowany w trakcie pierwszego etapu robót. Sterowanie przeciskiem i pomiar odbywa się przy wykorzystaniu monitora, na którym za pomocą kamery cyfrowej wyświetlany jest obraz diodowej tablicy celowniczej. Tablica ta umieszczona jest w tylnej części głowicy pilotowej.
Po osiągnięci przez głowice pilotową wykopu docelowego rozpoczyna się drugi etap pracy, tj. rozwiercanie otworu z jednoczesnym przeciskiem stalowych rur osłonowych. Urobek usuwany jest poprzez system przenośników ślimakowych umieszczonych w stalowych rurach osłonowych.
Po rozwierceniu otworu do żądanej średnicy i umieszczeniu w nim stalowych rur osłonowych następuje ostatni etap prac, czyli przecisk hydrauliczny rur przewodowych. Jako rury przewodowe stosuje się najczęściej rury kamionkowe, żelbetowe, z betonu polimerowego lub żywic poliestrowych. Możliwe jest również wciąganie rur z PE i PVC. Wciąganie rur z PE odbywa się po osiągnięciu przez głowicę pilotażową wykopu docelowego. Głowicę pilotażową wymienia się wówczas na głowice wciągającą i następuje wciąganie rur z PE do wykopu początkowego z jednoczesnym cofaniem żerdzi. Wciąganie rur z PVC możliwe jest po wykonaniu drugiego etapu robót i odbywa się ono z wykopu docelowego poprzez specjalna głowicę łączącą, jednocześnie z wyciąganiem rur osłonowych do wykopu początkowego.
Maszyna przewiertowa WPS 50 posiada sterowanie świdrem zapewniając dokładność (w pionie i w poziomie) układanego rurociągu. Maksymalna średnica rurociągu to 500 mm o długości roboczej do 60 metrów.
Metoda ta charakteryzuje się wysokim tempem robót, niskimi kosztami realizacji, prostą obsługą urządzenia, możliwością wykonania stosunkowo długich odcinków rurociągu oraz możliwością budowy rurociągu poniżej zwierciadła wody gruntowej.